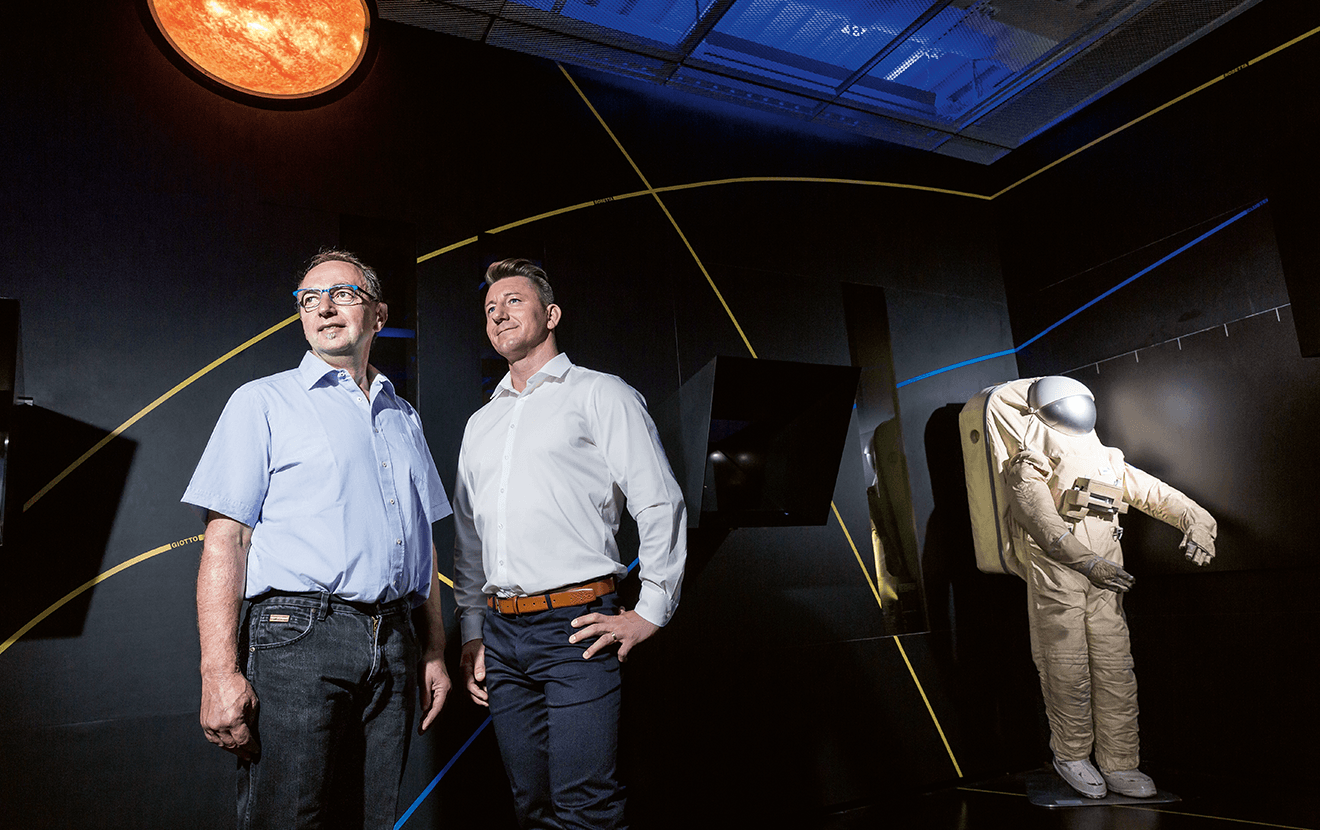
Space mission.
Exakt 3,30 Meter lang, 2,41 Meter hoch, rund zwei Meter tief: Der Container, der an einem Samstagabend im Frühling 2018 auf einer Palette ins Maindeck einer Boeing 777F von Lufthansa Cargo – Flugnummer LH8386 – mit Destination Tokio-Narita gleitet, ist unscheinbar. Doch er hat es in sich: eine hochempfindliche, 50 Millionen Euro teure Anlage für die Internationale Raumstation, kurz ISS. Dank der neuen Anlage dürfte die Chance auf bemannte Missionen zu weit entfernten Planeten wie dem Mars in nicht allzu ferner Zukunft deutlich steigen. Mitte September wurde die Anlage von Japan aus ins All geschossen. In der ISS übernahm Alexander Gerst die Montage – der Deutsche ist Kommandant der „Crew Expedition 57“ im Rahmen der aktuellen European-Space-Agency-Mission „Horizons“. Die Testphase des neuen Systems wird sich über ein ganzes Jahr erstrecken. „Raumfahrt ist für mich nicht nur ein Job, sondern ein Traum, den ich versuche zu leben“, sagt Denis Mitschke. „Deshalb war es toll, den Truck mit der Anlage an Bord wie geplant im Tanegashima Space Center ankommen zu sehen.“
Bis zur Übergabe an Japans Raumfahrtagentur JAXA war der 39-Jährige für alle Aufbau-, Integrations- und Testaktivitäten rund um die Anlage verantwortlich – im Auftrag von Airbus in Immenstaad am Bodensee. HOCHTECHNOLOGIE FÜR DIE ISS-CREWWas hat es mit dem Frachtstück auf sich? „Es ist ein neuartiges Lebenserhaltungssystem für Astronauten“, sagt der Diplom- Ingenieur Luft- und Raumfahrttechnik. „Unsere Anlage erzeugt etwa 40 Prozent des für den Elektrolyseprozess benötigten Frischwassers. Im Dauerbetrieb bedeutet dies eine jährliche Einsparung von bis zu 440 Kilogramm Wasser, die nicht von der Erde zur ISS transportiert werden müssen.“ Zudem benötigt sie viel weniger Platz als die älteren Anlagen. Das „Advanced Closed-Loop System“ (ACLS) hat drei Aufgaben, die in einem Reaktionskreislauf miteinander verbunden sind: 1. Wasser (H₂O) in Wasserstoff (H₂) und Sauerstoff (O₂) spalten und das O₂ den Astronauten zur Verfügung stellen; |
2. das von der Crew erzeugte Kohlenstoffdioxid (CO₂) entfernen; 3. Wasser erzeugen durch Zusammenführung des CO₂ und des H₂ aus den beiden anderen Prozessen in einer Reaktion, bei der als weitere Komponente Methan (CH₄) entsteht. Die Instrumente für all dies sind in ein kompaktes Regal verbaut. Den Auftrag erhielt Airbus 2011 von der ESA. „Aber die Entwicklung einzelner Komponenten hat schon vor über 20 Jahren begonnen“, sagt Andreas Kreis. Der Maschinenbau-Ingenieur war unter anderem verantwortlich für das „Engineering Model“, eine Art Zwilling des ACLS-„Flugmodells“, mit dem man die Abläufe im All am Boden nachvollziehen kann. Über die Jahre arbeiteten bei Airbus in Summe rund 150 Kollegen an dem System, darunter auch Chemiker oder Physiker. Das ACLS ergänzt in der Raumstation zwei seit Jahren genutzte Lebenserhaltungssysteme. Ausgelegt auf die Versorgung von drei Astronauten, soll das ACLS auch über den Test hinaus in der ISS bleiben – vorausgesetzt, es bewährt sich. |
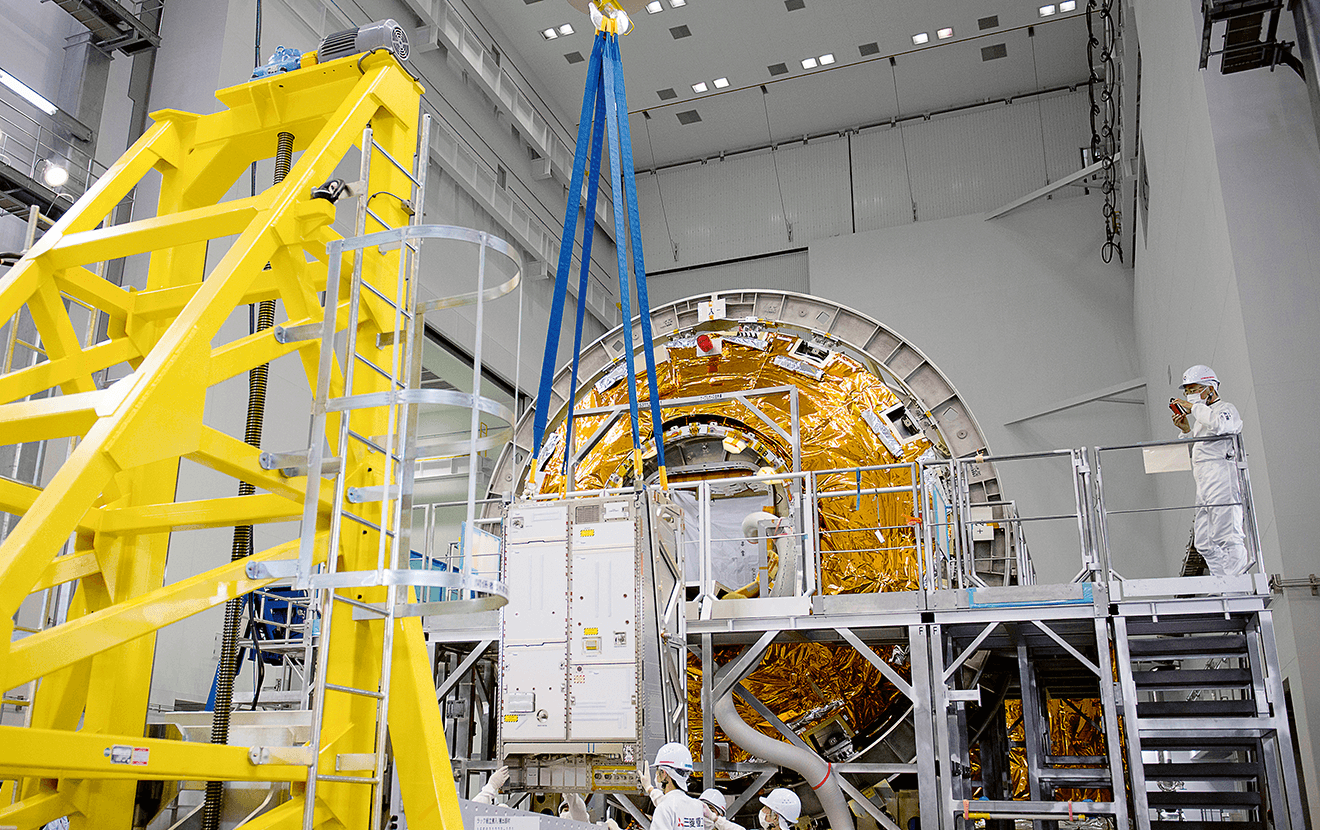
„Die Crew könnte damit theoretisch von derzeit sechs auf acht bis neun Mitglieder aufgestockt werden“, so Kreis. Vor allem aber soll die Weiterentwicklung hin zu einem komplett geschlossenen System gepuscht werden. „Ziel ist, das beim Wassererzeugen entstehende Methan nicht mehr wie bisher ins All zu leiten, sondern in Kohlen- und Wasserstoff zu spalten und den Kohlenstoff als Dünger zu nutzen“, erklärt Mitschke. Ein wichtiger Baustein im Lebenserhaltungssystem der ISS, mit dessen Hilfe man in der Raumstation Pflanzen anbauen könnte, die der Ernährung der Crew dienen. Das wiederum hieße: Die Astronauten könnten sich selbst versorgen und wären damit gewappnet für Mars-Reisen oder längere Aufenthalte auf dem Mond. Der Experte wagt eine vorsichtige Schätzung: „Ab 2030 könnte es einsatzfähig sein.“ Dramatisch kürzer fiel dagegen der Zeitrahmen beim Transport des ACLS durch Lufthansa Cargo und DB Schenker als Forwarder aus. „Die Sendung musste auf den Tag genau im Space Center ankommen“, sagt Kreis, der auch für die Logistik verantwortlich zeichnete. Der Start ins All erforderte umfangreiche Vorbereitungen durch die japanischen Experten. Schon deshalb war die Entscheidung für den Luftweg ohne Alternative. Und jene für „td.Flash“ – das Lufthansa Cargo Express-Produkt für Eiliges – konsequent. Hinzu kommt der Sicherheitsaspekt: „Beim Seetransport wäre das Risiko für Beschädigungen zu hoch gewesen.“
THERMO-TRUCKS UND COOL CENTER.
THERMO-TRUCKS UND COOL CENTER.
In den Monaten vor der Reise erarbeiten die Verantwortlichen bei Airbus mit ihren Transportpartnern einen Katalog an Schutzvorkehrungen. „Wir haben den Container von innen thermisch isoliert und mit reiner, trockener Luft acht Stunden lang gespült“, sagt Kreis. Vom Bodensee bis nach Japan wurde die Fracht durchgängig bei Temperaturen zwischen 15 und 25 Grad Celsius gehalten. Daher waren Thermo-Trucks auf den Straßenetappen das Transportmittel der Wahl. „In Frankfurt wurde das empfindliche Frachtstück bis zum letztmöglichen Zeitpunkt im |
Lufthansa Cargo Cool Center (LCCC) gelagert. Die besonders überwachte Verladung in den Frachter erfolgte in kürzester Zeit. In Japan wurde vergleichbar verfahren“, sagt Michael Butz, Projektverantwortlicher beim Frachtkranich. „Jeder Mitarbeiter wusste genau um seine Verantwortung.“ Erfahrung mit solchen Spezialprojekten für den Weltraum hatte Lufthansa Cargo zuletzt vor wenigen Monaten beim Transport eines Satelliten nach Kalifornien gesammelt (s. „planet“ 2/2017). |
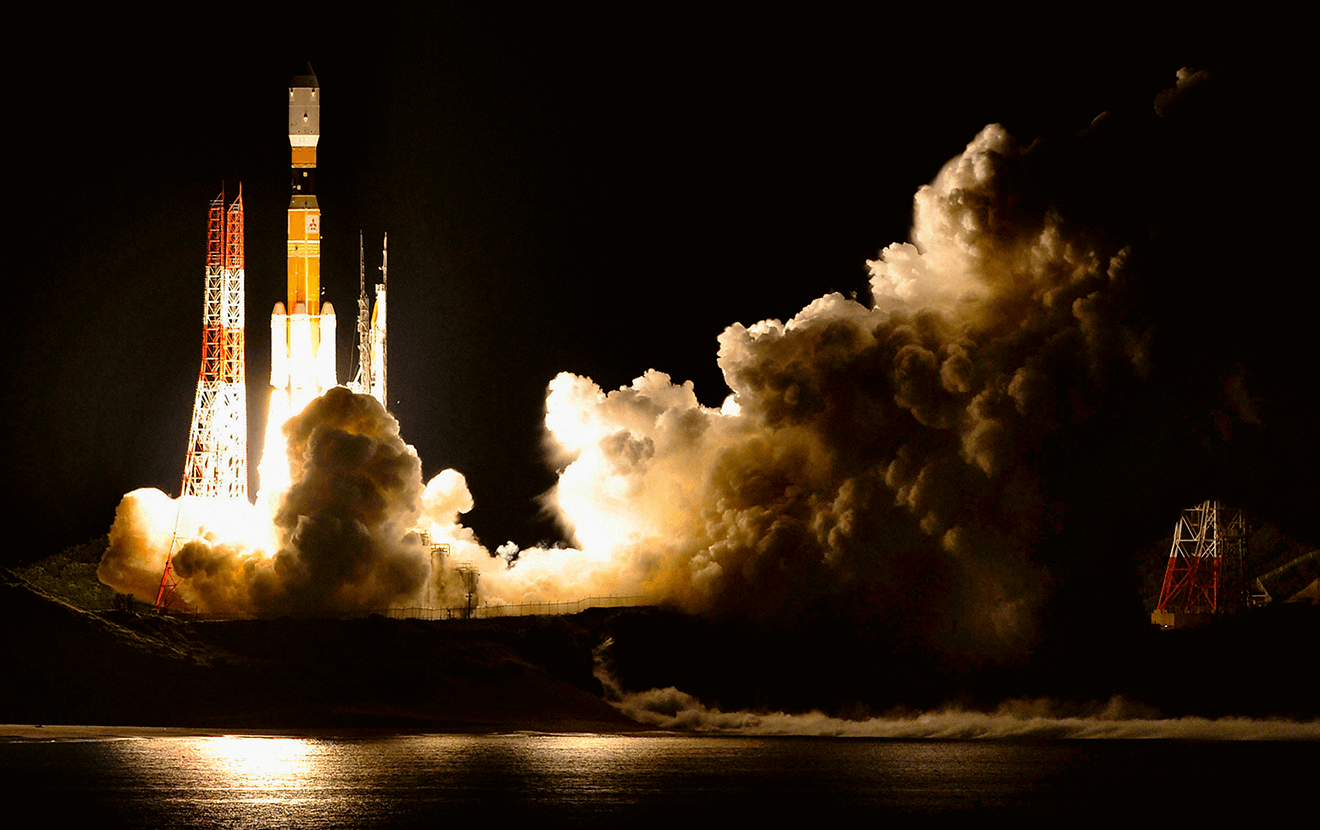
Mit einer Boeing 777F hob das ACLS im Rahmen des Spezialprodukts „Cool“ ab. Der beim Flug herrschende Unterdruck wurde mit Ventilen ausgeglichen – nachdem durch Analysen feststand, dass die Luft im Frachtraum den Reinheitskriterien entspricht. Um Stöße zu dämpfen, lagerte das Regal mit dem System im Container auf vier Federn. „Lufthansa Cargo und auch DB Schenker haben eingespielte Teams und konnten uns einen End-to-end-Service anbieten. Der Transport ist absolut reibungslos verlaufen“, sagt Denis Mitschke anerkennend. So richtig begeistert klingt er dann aber freilich doch erst, als er den Start der Trägerrakete beschreibt: „Die Kraft zu spüren, die bei einem Launch entwickelt wird, das ist ein Wahnsinnserlebnis!“