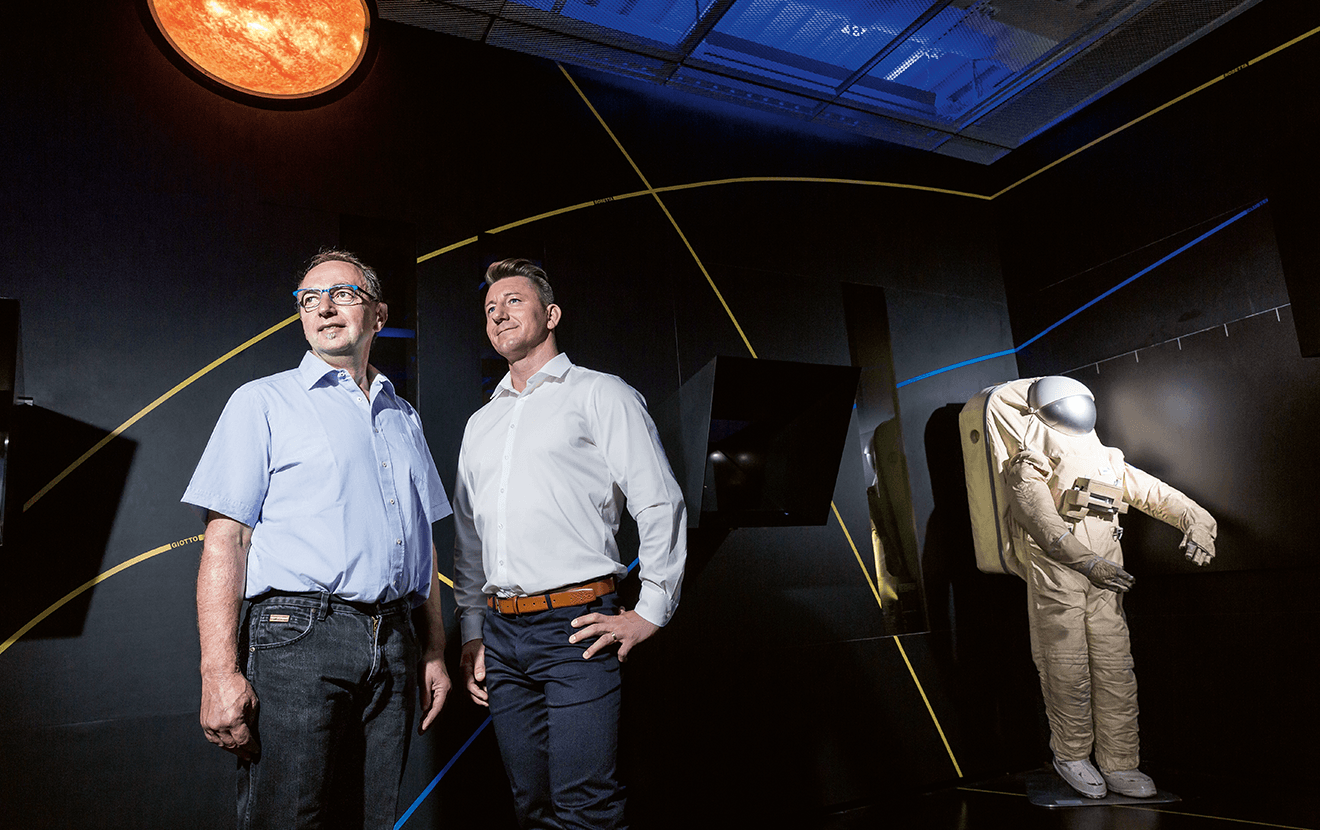
Space mission.
Exactly 3.30 meters long, 2.41 meters high, about two meters deep: the container mounted on a pallet that is sliding onto the main deck of a Lufthansa Cargo Boeing 777F – flight number LH8386, destination Tokyo Narita – on a Saturday evening in spring 2018 looks rather inconspicuous. But there is more to it than meets the eye: it contains highly sensitive and sophisticated equipment worth 50 million euros, intended for use on the International Space Station, or ISS for short. Thanks to the new equipment, the chances of mounting manned missions to far-away planets such as Mars in the not too distant future could be boosted significantly. In mid-September, the new system was launched into space from Japan. In the ISS, Alexander Gerst took care of the assembly – the German is the commander of the “Crew Expedition 57”, which is part of the current European Space Agency mission “Horizons”. Testing of the new system will extend over a whole year. “To me, space travel is not just a job; it’s a dream I’m trying to make come true,” says Denis Mitschke.
“That’s why it was so great to see the truck carrying the equipment arrive at the Tanegashima Space Center as planned.” Until the handover to Japan’s space agency JAXA, the 39-year-old was responsible for all assembly, integration and test activities for the system – working on behalf of Airbus in Immenstaad on Lake Constance. CUTTING-EDGE TECHNOLOGY FOR THE ISSSo what is the story with this piece of cargo? “It is a new type of life-support system for astronauts,” says the aerospace engineer. “Our plant produces about 40 percent of the fresh water required for the electrolysis process. Once it is in continuous operation, this will translate into up to 440 kilograms of water per year that do not have to be transported from Earth to the ISS.” It also has a much smaller footprint than the previous systems. The Advanced Closed-Loop System (ACLS) has three tasks that are linked in a reaction cycle: 1. split water (H₂O) into hydrogen (H₂) and oxygen (O₂) and |
provide O₂ to the astronauts; 2. remove the carbon dioxide (CO₂) produced by the crew; 3. produce water by combining CO₂ and H₂ from the other two processes in a reaction that produces methane (CH₄) as a by-product.The instruments controlling all these processes are built into a compact rack. Airbus was commissioned by the ESA in 2011. “But the development of individual components began more than 20 years ago,” says Andreas Kreis. Among other things, the mechanical engineer was responsible for the “Engineering Model”, a kind of twin of the ACLS “flight model”, which can reproduce the processes in space back here on Earth. Over the years, a total of around 150 colleagues have worked on the system at Airbus, and they included chemists and physicists. The ACLS complements two life-support systems that have been installed in the space station for years. Designed to provide life support for three astronauts, the ACLS is intended to remain on the ISS once testing is completed – provided it passes the tests. |
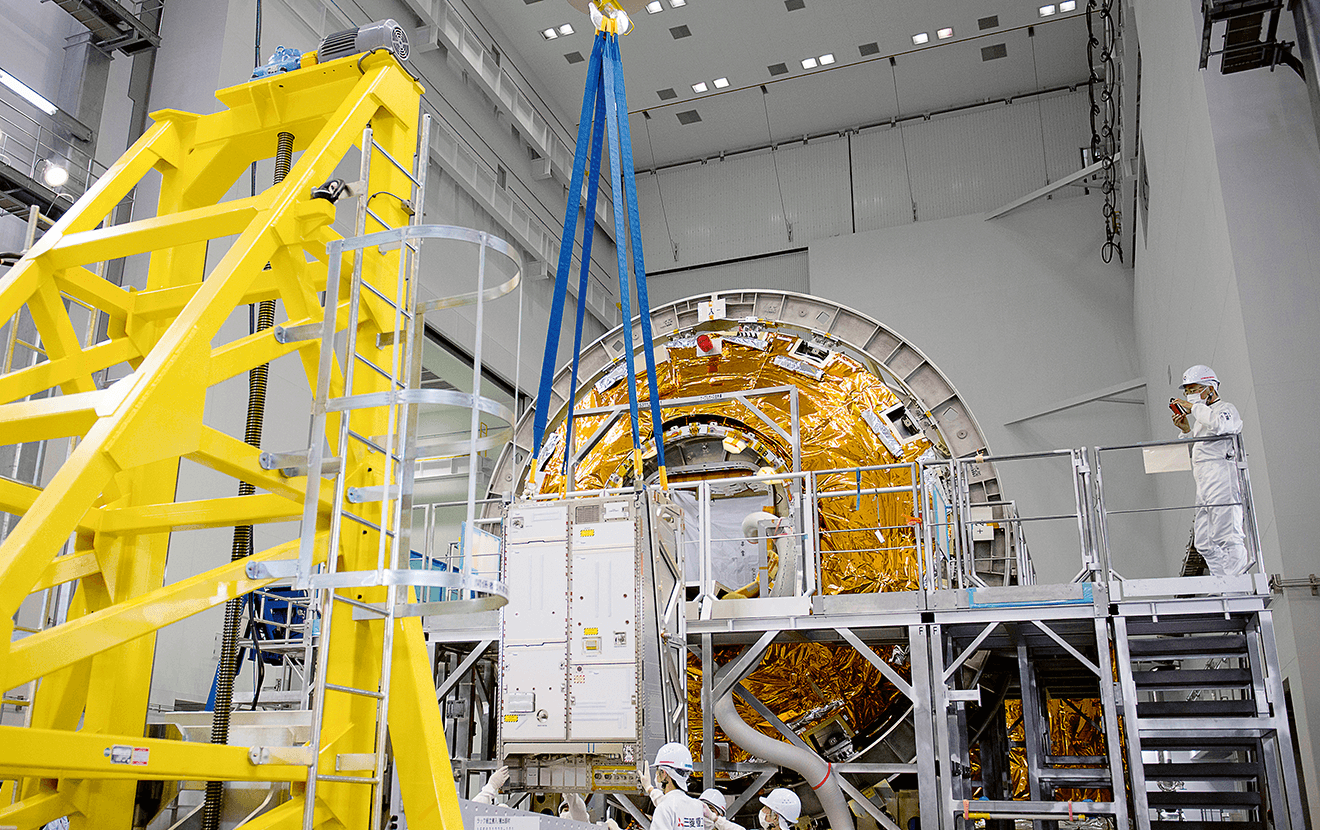
This would in theory allow the crew to be increased from the current six to eight or nine members.” However, the main goal is to pursue the further development towards a completely closed system. “The aim is now no longer to dispose of the methane generated when producing water, by releasing it into space; now the goal is to split it into carbon and hydrogen and then use the carbon as fertilizer,” explains Mitschke. It is an important component of the ISS life-support system and would allow plants to be cultivated inside the space station, these would help feed the crew. This in turn would mean that the astronauts would become self-sufficient and thus be ready for journeys to Mars, or for longer stays on the moon. The expert’s cautious estimate: “It could be ready for deployment by 2030.” A much shorter time span was needed for the transport of the ACLS by Lufthansa Cargo and DB Schenker as forwarding agency. “The shipment had to arrive at the Space Center right on time,” says Kreis, who was also responsible for logistics. That required extensive preparations on the part of the Japanese experts. For this reason alone, there was no viable alternative to airfreight. Or to “td.Flash” – the Lufthansa Cargo Express product for urgent shipments. There was also the added safety aspect: “With seafreight, the risk of damage would have been too high.”
THERMO TRUCKS AND COOL CENTER.
THERMO TRUCKS AND COOL CENTER.
In the months leading up to the journey, the people in charge at Airbus and their transport partners prepared a catalog of protective measures. “We installed thermal insulation inside the container and then ventilated it using purified, dry air for eight hours,” says Kreis. From Lake Constance to Japan, the cargo was kept at temperatures between 15 and 25 degrees Celsius. For this reason, temperature-controlled trucks were the chosen means of transportation on the road. “In Frankfurt, the sensitive cargo was kept in storage in the Lufthansa Cargo Cool Center, the LCCC, |
until the last possible moment. The specially supervised loading process into the freighter was accomplished in record time. A similar procedure was used in Japan,” says Michael Butz from Lufthansa Cargo, who was responsible for the project. “All employees were very clear about their individual responsibilities.” The last time Lufthansa Cargo was involved in a special aerospace project was a few months ago when transporting a satellite to California (see “planet” 2/2017). |
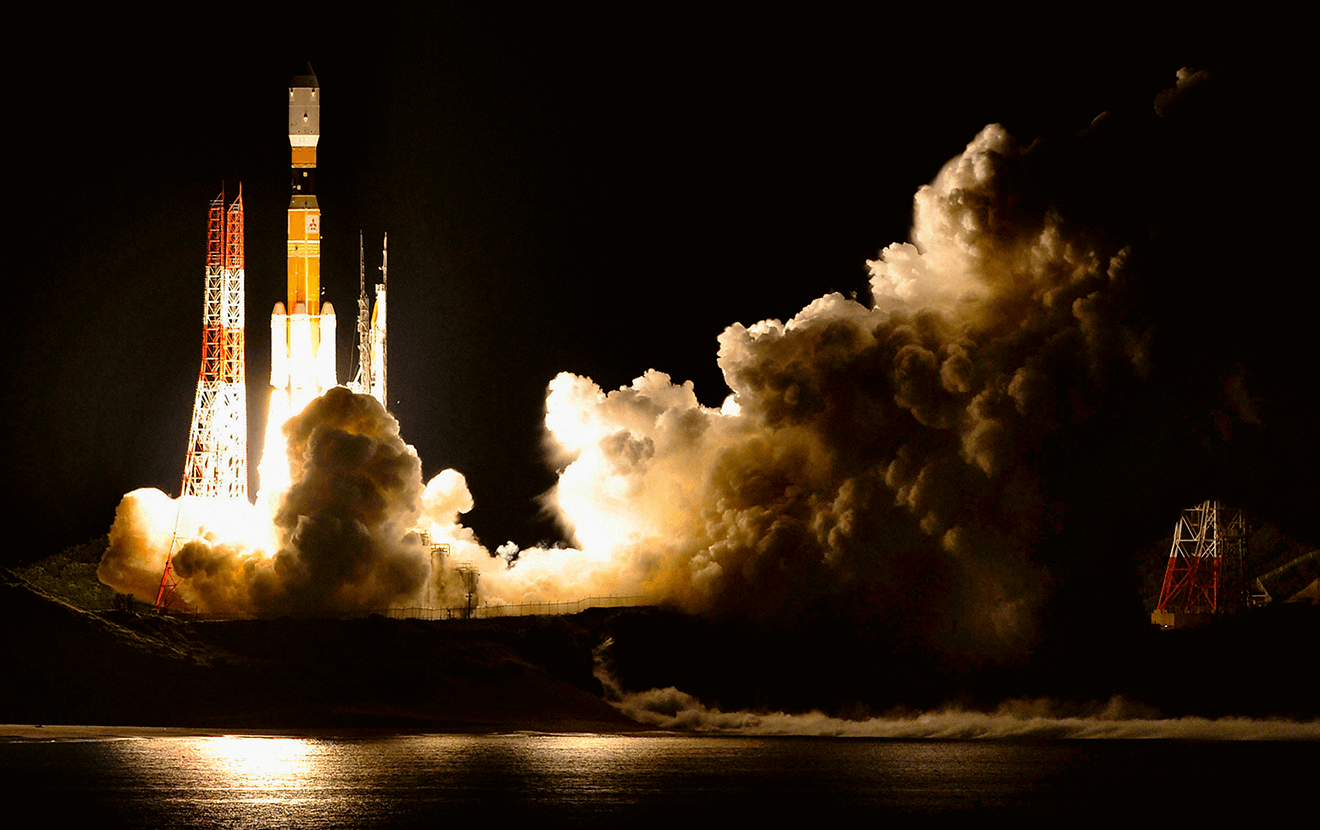
The ACLS took off on a Boeing 777F, shipped using the special product “Cool”. The negative pressure prevailing during the flight was compensated by means of valves – once analyses had shown that the air in the cargo compartment met the purity criteria. In order to dampen the shocks, the rack holding the system inside the container rested on four springs. “Both Lufthansa Cargo and DB Schenker have experienced teams, and they offered us end-to-end service. The transport went absolutely smoothly,” says Denis Mitschke. Yet it is only when he describes the moment when the launch vehicle lifted off that he gets really excited: “To feel the power that is generated during a launch is an extraordinary experience!”